Development of wireless sensor node hardware for large-area capacitive strain monitoring
An alternating current(AC) bridge based wireless capacitive strain sensor development and realworld implementation for I-70 steel girder bridge fatigue monitoring
Conventional resistive-type strain sensing methods have limitations in large-area sensing due to their relatively small size. The soft elastomeric capacitive (SEC) sensor is a capacitance-based stretchable electronic strain sensor developed by Prof. Simon Laflamme in the Iowa state university. SEC has shown distinct advantages for mesoscale sensing over conventional strain-based structural health monitoring (SHM) due to its wide surface coverage capability.
Recent studies have demonstrated that the SEC sensor has linearity up to measuring 20% strain and sufficient durability for structural crack monitoring, promising the performance in mesoscale sensing of static/dynamic strain responses for both concrete and steel structures While recent advances in wireless sensor technologies have provided an attractive alternative to wired and centralized SHM, the capacitive strain sensing methods have not benefitted from the wireless approaches due to the lack of appropriate hardware element. This study develops a wireless sensor board to use the SEC sensor in combination with a wireless sensor network for SHM by addressing key implementation challenges.
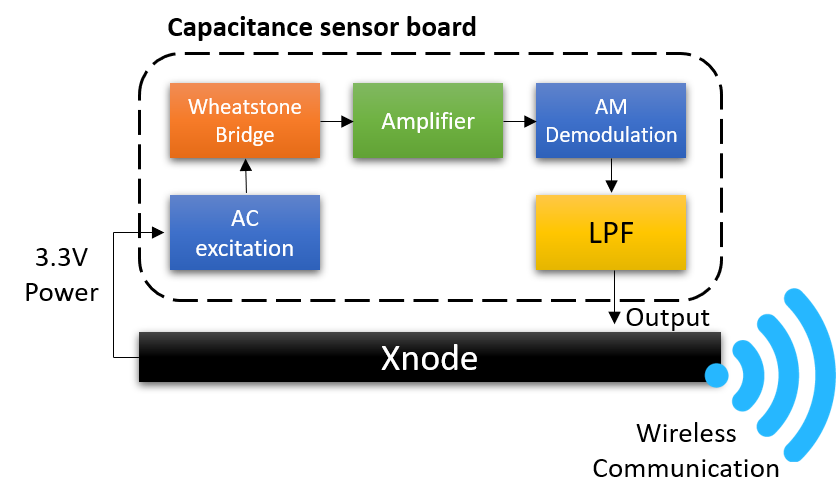
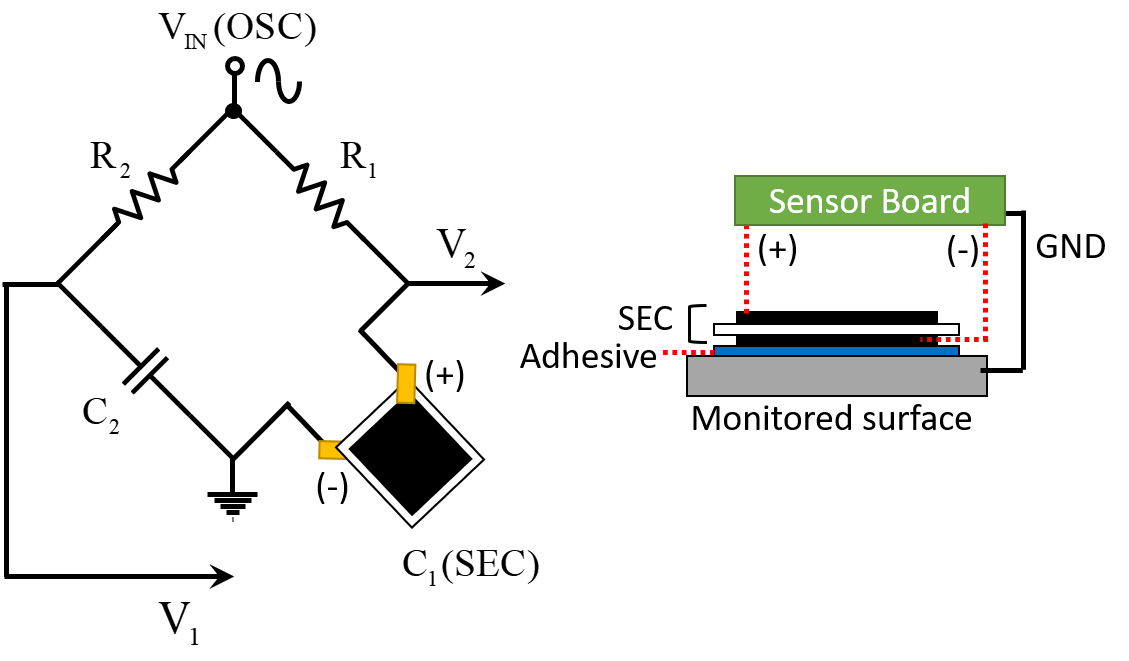
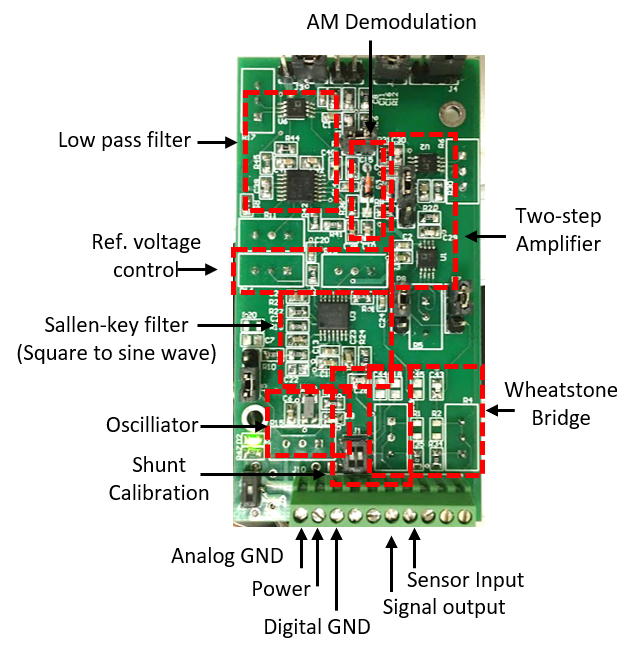
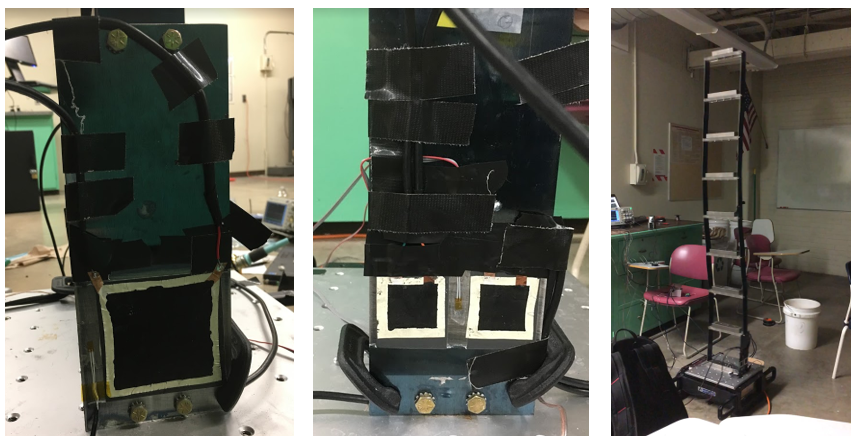
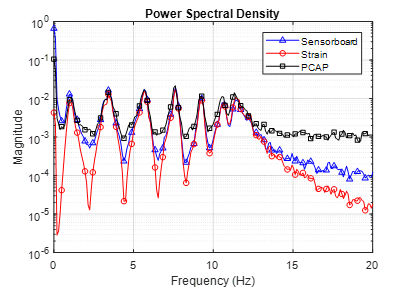
A 20 Hz band-limited white noise was used for the test excitation. A 3 × 3 in. SEC was used for performance evaluation. Foil-type strain gauge(resistive), SEC measured from PCAP02(i.e., commercial wired capacitance sensing system), and sensorboard connected interfaced with wireless sensor node(i.e., Xnode, embedor tech). The leftmost figure shows a comparison of the measurements in the frequency domain. In particular, power spectral density was used to evaluate the noise floor of each data. All three measurements successfully identified the natural frequency peaks of the shear building, but showed differences in the noise floor. As seen in figure, the strain gauge data showed the clearest peaks with the lowest noise level. The SEC measurements from both the PCAP02 and the sensor board captured the natural frequency peaks clearly but showed higher noise floor levels. Nonetheless, as expected, the sensor board showed better noise performance than the PCAP02 over the whole frequency range.
Two-step shunt calibraiton strategy
For practical applications of the sensor board, a calibration process that converts the voltage output from the Wheatstone bridge into absolute capacitance value is required. A traditional shunt calibration approach that uses a single additional capacitor, however, does not provide accurate calibration because the parasitic resistance and capacitance of lead wires connected to the SEC sensor can cause substantial signal drift issue. In order to eliminate this side effect due to the long lead wire impedance, a modified shunt calibration method that uses dual-step calibration process is proposed in this study.

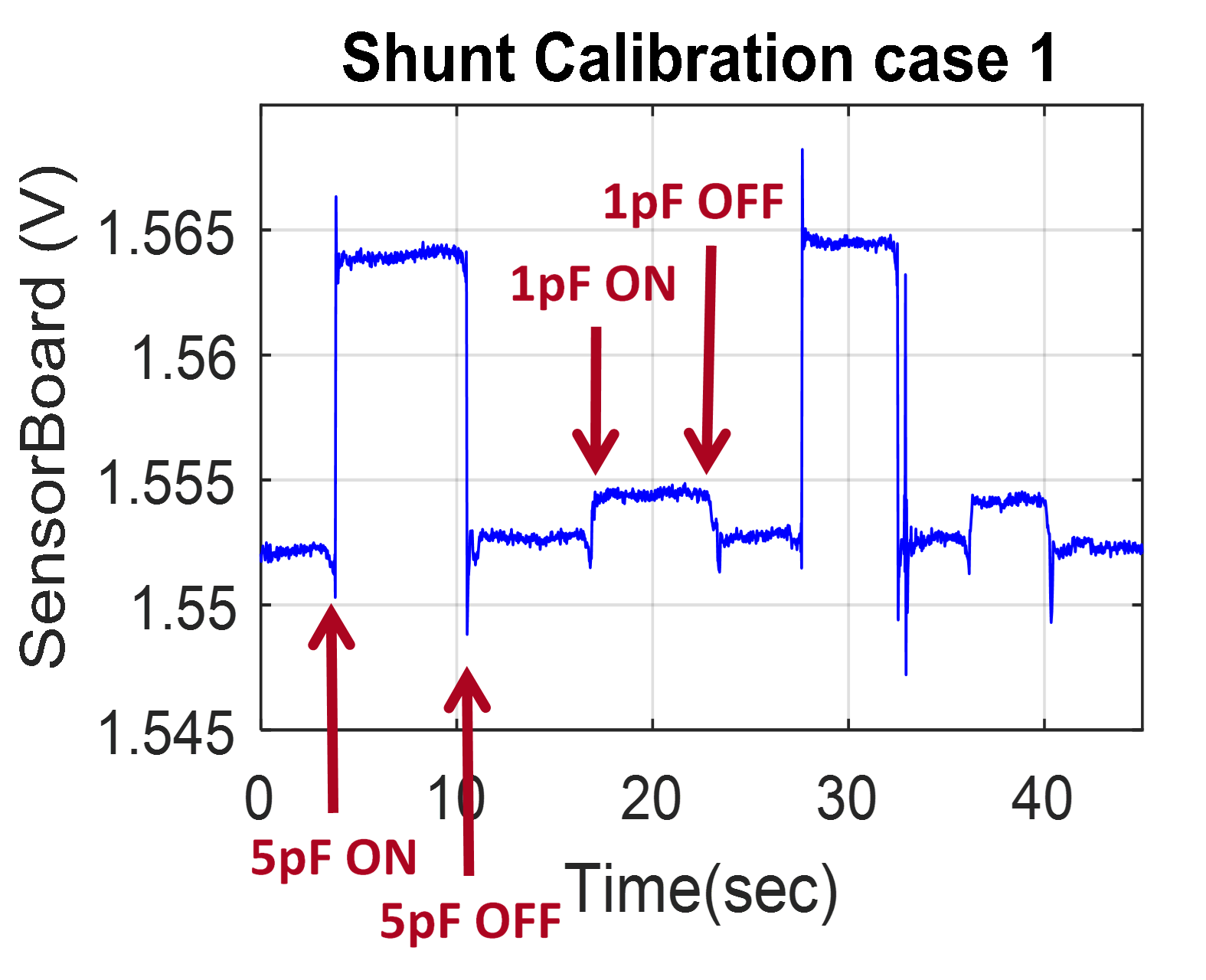
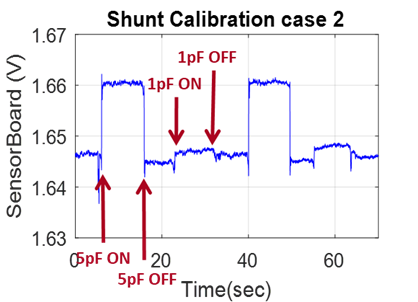
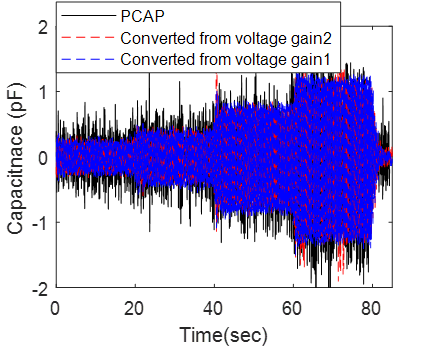
The proposed shunt calibration process and its calibration factor successfully converted the different voltage output signals from the two cases into the actual capacitance change.
More details can be found in the published paper below:
Jeong, J. H., Xu, J., Jo, H., Li, J., Kong, X., Collins, W., … & Laflamme, S. (2018). Development of wireless sensor node hardware for large-area capacitive strain monitoring. Smart Materials and Structures, 28(1), 015002. Click here!